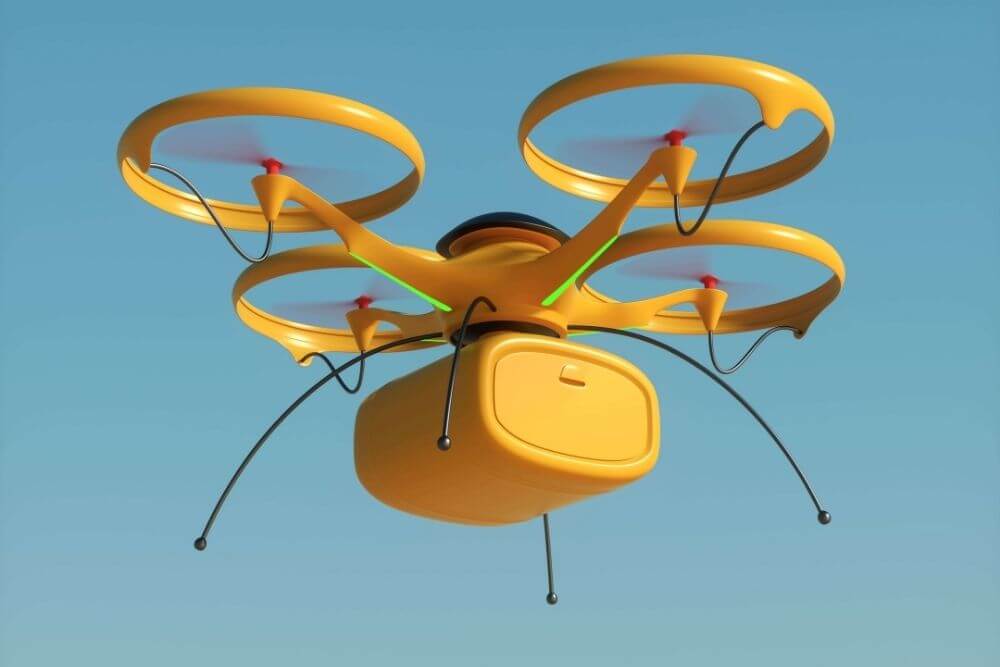
Injection molding vs 3D printing
When it comes to manufacturing, two of the most common production techniques are injection molding and 3D printing. Both methods have their strengths and weaknesses, making them suitable for different applications. Whether you’re a business looking to scale production or an individual prototyping a new product, understanding the key differences between these processes will help you make the best decision.
What is Injection Molding?
Injection molding is a manufacturing process in which molten material—typically plastic—is injected into a mold cavity. Once the material cools and solidifies, the finished part is ejected. This process is widely used for mass production due to its efficiency and consistency.
Advantages of Injection Molding:
- High Volume Production: Injection molding is ideal for producing large quantities of identical parts.
- Durability and Strength: Parts made using injection molding tend to be stronger than 3D-printed parts.
- Material Variety: A wide range of materials, including thermoplastics, elastomers, and some composites, can be used.
- Surface Finish: The process produces smooth, high-quality surfaces that often require minimal post-processing.
Disadvantages of Injection Molding:
- High Initial Costs: Tooling and mold production can be expensive, making it less viable for small runs.
- Longer Lead Times: Designing and manufacturing molds can take weeks or months.
- Limited Design Flexibility: Complex geometries may require expensive molds or be impossible to produce.
What is 3D Printing?
3D printing, or additive manufacturing, builds parts layer by layer using digital models. Various 3D printing technologies exist, including Fused Deposition Modeling (FDM), Stereolithography (SLA), and Selective Laser Sintering (SLS), each with unique capabilities.
Advantages of 3D Printing:
- Low Initial Cost: No expensive molds or tooling required, making it cost-effective for small runs and prototyping.
- Design Flexibility: Allows for highly complex and intricate designs that are difficult or impossible to achieve with injection molding.
- Rapid Prototyping: Quick turnaround time enables faster iteration and product development.
- Customization: Each piece can be uniquely tailored without additional costs.
Disadvantages of 3D Printing:
- Limited Production Speed: 3D printing is slower compared to injection molding, making it less suitable for mass production.
- Material Limitations: While the range of materials is growing, it is still not as diverse as what’s available for injection molding.
- Surface Finish and Strength: Printed parts may require post-processing to achieve a smooth surface, and they tend to be weaker than injection-molded parts.
Choosing the Right Process
Use Injection Molding If:
- You need to produce large quantities of the same part.
- Strength and durability are critical factors.
- You want a professional surface finish with minimal post-processing.
- You can afford high upfront tooling costs.
Use 3D Printing If:
- You are in the prototyping or early-stage development phase.
- Your design is complex and may require multiple iterations.
- You need a small production run with minimal upfront investment.
- Customization is a key factor for your product.
Final Thoughts
Both injection molding and 3D printing have their place in modern manufacturing. If you need high-volume production with a polished finish, injection molding is the way to go. However, if you need flexibility, quick iteration, and cost-effectiveness for small runs, 3D printing is a powerful alternative.
At 3D et cetera, LLC, we specialize in both 3D printing and prototyping, helping businesses and individuals bring their ideas to life. Whether you’re developing a one-off prototype or planning for mass production, we can guide you in choosing the best process for your needs. Contact us today to discuss your project!